Maximizing Efficiency with Liquid Silicone Injection Molding Machines
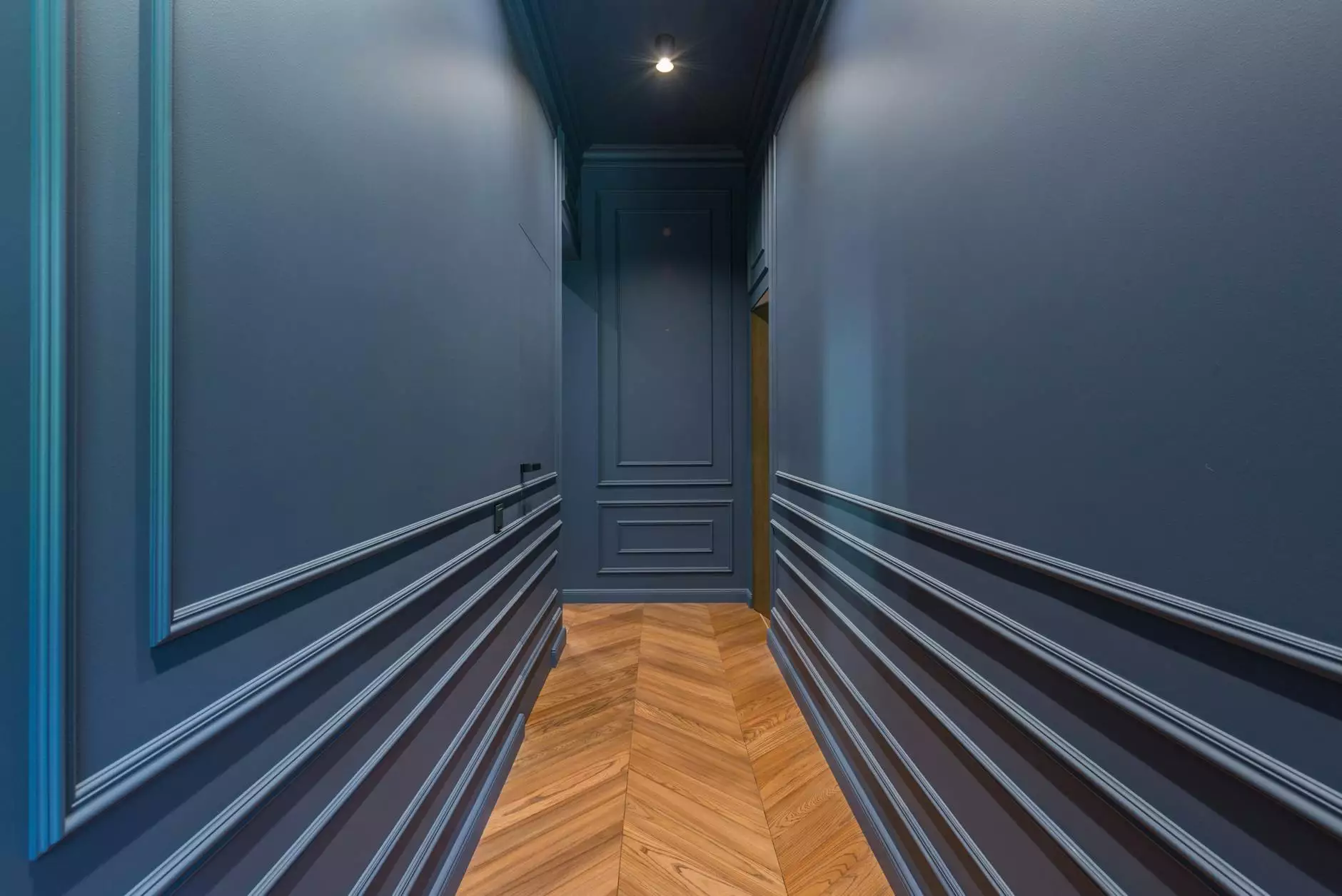
The evolving landscape of manufacturing, particularly in the electronics and medical supplies sectors, continues to demand innovative and efficient production solutions. One revolutionary technology making waves is the liquid silicone injection molding machine. These machines are not only enhancing product quality but also significantly improving operational efficiency. In this article, we will explore the advantages, applications, and future of liquid silicone injection molding machines, particularly focusing on their integration within Nolato's esteemed product offerings.
Understanding Liquid Silicone Injection Molding
Liquid silicone rubber (LSR) is a versatile material known for its elasticity, temperature resistance, and biocompatibility, making it ideal for various applications. The process of liquid silicone injection molding involves the injection of liquid silicone into molds, where it undergoes curing to obtain a solid state. This method is vastly different from traditional molding techniques and offers numerous benefits, such as:
- Precision and Detail: LSR can capture intricate designs and details due to its low viscosity.
- Cost-Effectiveness: High production rates reduce per-unit costs, making it suitable for large scale manufacturing.
- Flexibility: The ability to create complex shapes and designs without extensive re-tooling.
- Durability: Products made from LSR are resistant to extreme temperatures and harsh environments.
Applications in Electronics
The electronics industry constantly seeks materials that enhance product performance while ensuring longevity. The liquid silicone injection molding machine has become a preferred choice for manufacturers because:
Improved Sealing and Insulation
One of the most significant applications of LSR in electronics is in the production of seals and insulation components. Due to its excellent electrical insulation properties, LSR helps in:
- Reducing the risk of electrical failures.
- Providing superior moisture protection for sensitive components.
- Contributing to lightweight designs without compromising on strength.
Integration into Wearable Technology
The rise of wearable technology necessitates the use of flexible yet durable materials. Liquid silicone injection molding machines enable manufacturers to produce:
- Comfortable bands and straps that mold to the wearer's wrist.
- Seamless designs tailored for aesthetics and functionality.
This not only enhances the user experience but also broadens the product's appeal in the competitive market.
Transforming Medical Supplies
In the medical field, reliability and safety are paramount. Liquid silicone rubber's biocompatibility makes it suitable for manufacturing various medical devices and supplies. Here’s how:
Medical Device Components
Liquid silicone injection molding machines can produce components such as:
- Catheters and tubing that require high flexibility and biocompatibility.
- Seals and gaskets for medical devices that must maintain sterility and safety.
This capability ensures that manufacturers can meet stringent regulatory requirements while delivering high-quality products.
Consumer Health Products
The rise in consumer health awareness has led to an increased demand for health-related gadgets. Liquid silicone injection molding allows for:
- Customizable products, from thermometer covers to hygienic surfaces.
- High-volume production of disposable items without sacrificing quality.
Advantages of Investing in Liquid Silicone Injection Molding Machines
Investing in liquid silicone injection molding technology provides numerous benefits for businesses, particularly those in the electronics and medical sectors:
High Efficiency and Speed
The machinery is designed for rapid production cycles, significantly reducing time to market. This is particularly beneficial for businesses like Nolato, which thrive on innovation and speed.
Reduced Waste
Liquid silicone injection molding produces minimal waste compared to traditional molding processes. The process is highly efficient and utilizes only what is necessary, resulting in:
- Lower material costs.
- Enhanced sustainability practices.
Quality Control and Consistency
With advanced technology and precise controls, businesses can ensure that each product meets their quality specifications consistently. For Nolato, this commitment to quality enhances brand reputation and customer satisfaction.
Case Study: Nolato’s Implementation of Liquid Silicone Injection Molding Machines
Nolato has been at the forefront of utilizing cutting-edge technology in manufacturing. By integrating liquid silicone injection molding machines into their production line, Nolato has achieved remarkable results:
Customized Solutions for Clients
By leveraging the flexibility of LSR, Nolato can offer tailored solutions that meet client-specific needs, enhancing customer loyalty and driving business growth.
Meeting Regulatory Standards
Nolato has successfully adapted its manufacturing processes to comply with stringent medical device regulations, ensuring that all products are safe, reliable, and of the highest quality.
The Future of Liquid Silicone Injection Molding Technology
The future of liquid silicone injection molding is bright, with continued advancements expected in technology and applications. Noteworthy trends include:
- Automation: Further integration of automation technologies will enhance productivity and accuracy.
- Innovation in Materials: Ongoing research will lead to even more specialized silicone materials with enhanced properties.
- Sustainability Focus: As industries shift towards greener practices, LSR’s recyclability and lower waste production will drive its adoption.
Conclusion
In conclusion, the liquid silicone injection molding machine is a game-changer in the manufacturing landscape, especially for industries such as electronics and medical supplies. Nolato stands as an exemplary model of how embracing this technology can lead to improved efficiency, better product quality, and enhanced customer satisfaction. As the industry advances, those who invest in innovative technologies like LSR will undoubtedly remain ahead of the curve.