Understanding Plastic Mold Manufacturing: Innovations and Insights
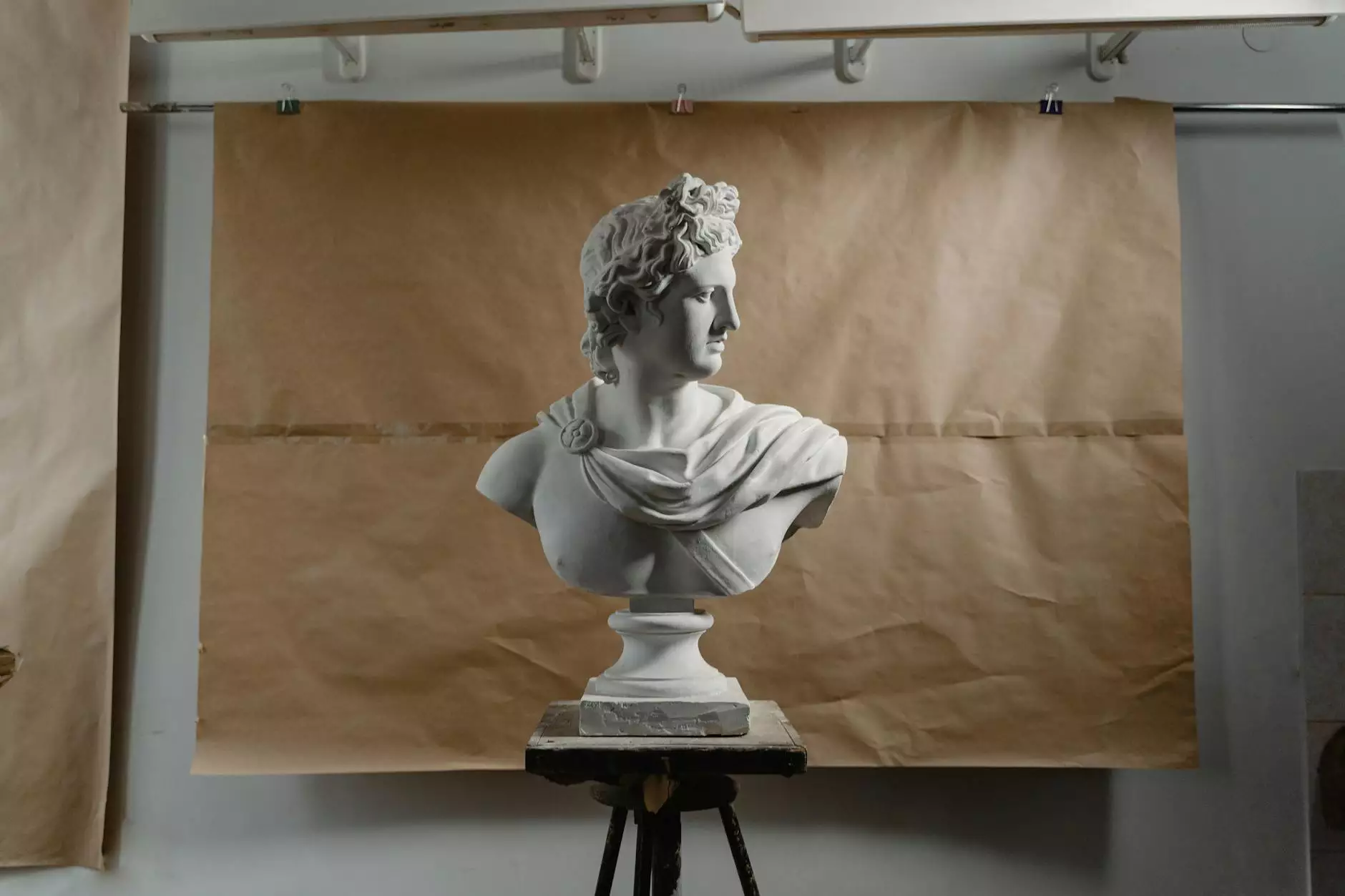
The plastic mold manufacturing industry is a cornerstone of modern manufacturing, providing essential components for countless products we use in our daily lives. From automotive parts to consumer electronics, the significance of precision molding cannot be overstated. In this comprehensive guide, we delve into the intricacies of plastic mold manufacturing, examining its processes, benefits, and innovations.
What is Plastic Mold Manufacturing?
At its core, plastic mold manufacturing is a process that involves creating plastic parts by injecting molten plastic into a mold. This method is highly efficient and allows for the mass production of complex geometries with minimal waste. The industry has significantly evolved, enabling manufacturers to produce high-quality components rapidly.
The Process of Plastic Mold Manufacturing
The plastic mold manufacturing process can be broken down into several key stages:
- Design Phase: The journey begins with a meticulously crafted design. Engineers use Computer-Aided Design (CAD) software to create a 3D model of the desired part, ensuring accuracy and functionality.
- Mold Creation: The next step involves crafting the mold itself, usually from steel or aluminum. High precision machining techniques are applied to manufacture the mold, resulting in seamless cavities that mirror the desired product.
- Injection Phase: Once the mold is ready, plastic granules are heated until they become molten. This liquid plastic is then injected into the mold under high pressure, filling every cavity to form the part.
- Cooling and Ejection: As the molten plastic cools, it solidifies into the shape of the mold. Once cool, the mold opens, and automated systems eject the finished part.
- Finishing Touches: The final step often includes trimming, painting, or adding additional features to the component to meet product specifications.
Benefits of Plastic Mold Manufacturing
There are numerous benefits to employing plastic mold manufacturing techniques, particularly when contrasted with other manufacturing methods. Here are some key advantages:
- Cost-Effectiveness: Once the initial mold is created, the cost per part decreases with larger production runs. The process is economical for large-scale manufacturing.
- High Precision: Advanced technology allows for exceptionally high precision, resulting in parts that meet strict tolerances and specifications.
- Versatility: Plastic molds can accommodate a wide variety of materials, enabling manufacturers to select the best material for each application.
- Fast Production Times: The injection molding process is rapid, significantly reducing lead times and enabling quick turnaround on product development.
- Low Waste: The process is highly efficient, with minimal material waste during production.
Innovations in Plastic Mold Manufacturing
The plastic mold manufacturing industry is constantly evolving, with innovations that enhance efficiency and product quality. Some of the recent advancements include:
1. Additive Manufacturing Integration
Additive manufacturing, commonly known as 3D printing, is being integrated with traditional plastic mold manufacturing. This combination allows for rapid prototyping of molds, leading to shorter development timelines and increased flexibility in design changes.
2. Advanced Materials
The introduction of advanced materials, such as bio-based or recycled plastics, is reshaping the industry. These materials provide sustainable options without compromising on quality and durability.
3. Automation and Robotics
Automation and robotics are playing a significant role in optimizing the plastic mold manufacturing process. Automated systems enhance production speeds, improve consistency, and minimize human error.
4. Smart Manufacturing Technologies
Embracing smart manufacturing technologies, including IoT and data analytics, allows manufacturers to monitor machinery performance in real-time, predict maintenance needs, and optimize production schedules.
Applications of Plastic Mold Manufacturing
The applications for plastic mold manufacturing are vast. Some of the most notable sectors include:
1. Automotive Industry
The automotive industry relies heavily on plastic parts for components such as dashboards, exterior trims, and under-the-hood applications. The lightweight nature of plastic contributes to overall vehicle efficiency and performance.
2. Consumer Products
From kitchenware to electronics, plastic mold manufacturing produces an array of consumer products. The ability to create intricate designs at scale meets the demands of consumer preferences for aesthetics and functionality.
3. Medical Devices
In the medical field, plastic mold manufacturing is essential for producing disposable devices, surgical components, and drug delivery systems. The precision involved is vital for ensuring safety and effectiveness.
The Importance of Quality Control in Plastic Mold Manufacturing
Quality control is paramount in the plastic mold manufacturing process. Manufacturers must implement meticulous inspection procedures to ensure that every part meets rigorous industry standards. Quality assurance practices include:
- Material Inspection: Ensuring that raw materials meet quality specifications before entering production.
- Process Monitoring: Continuously monitoring the injection molding process to detect any deviations from the norm.
- Final Product Testing: Conducting tests on finished products to check for defects and confirm compliance with design specifications.
Choosing the Right Partner for Plastic Mold Manufacturing
When selecting a manufacturing partner, it’s essential to consider their expertise, technology, and reputation in the industry. For businesses seeking excellence in plastic mold manufacturing, companies like DeepMould.net provide invaluable support. They offer:
- Experienced Engineers: A team of professionals with in-depth knowledge of design and manufacturing processes.
- State-of-the-Art Facilities: Advanced machinery and technology that ensure high-quality production.
- Customer-Centric Approach: A commitment to understanding and meeting clients’ unique requirements.
Conclusion
In conclusion, plastic mold manufacturing is a dynamic and essential field that drives innovation across numerous industries. With its cost-effectiveness, precision, and versatility, it plays a critical role in producing high-quality products that meet the demands of today's market. As the industry continues to evolve, advancements in technology and materials will only enhance the capabilities of plastic mold manufacturing, paving the way for exciting new applications and opportunities.
By understanding the complexities and benefits of plastic mold manufacturing, businesses can better position themselves in the marketplace and leverage the strengths of this vital manufacturing process. Whether you’re in need of small-scale production or large-volume runs, engaging with experienced partners like DeepMould.net will ensure your manufacturing needs are met with excellence and efficiency.